
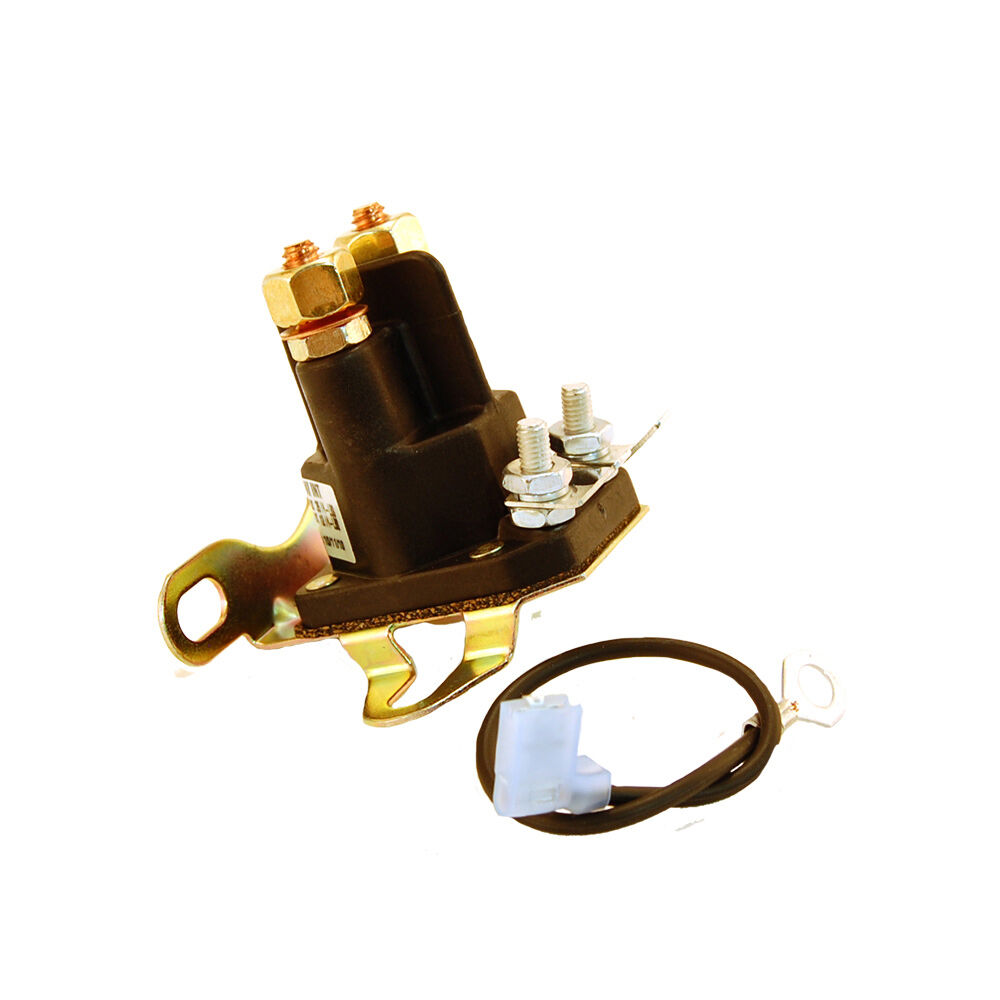
Tears in the diaphragm are usually an indication of over pressure. Identifying the root cause of a failure can be difficult as a number of factors may be involved but the following can be used as a guide.Įxceeding the pressure rating of the solenoid valve can cause damage to the valve components. Valve failure can be avoided if the valve is installed and maintained correctly and is operated within the limits of the specifications.

V-Flow Solutions sister company M&M International UK Ltd can offer a wide range of replacement solenoid coils. Installing the valve with the coil and armature positioned vertically is also recommended as this reduces the risk of sediment falling into the tube.īurnt out or damaged solenoid coils should be replaced. To prevent impurities entering the valve an upstream filter should be fitted into the system. The coil will continue to attempt to move the armature but, because of the restriction, will eventually overheat. If the particles are allowed into the armature tube, they may restrict the movement of the armature. Sediment or other particles entering the valve may cause coil failure. These should be inspected regularly and if damaged or worn should be replaced. Certain solenoid valves are fitted with armature tube o-rings which help to prevent water ingress between the coil and armature tube. If fitted with a suitable DIN connector the coil has an Ingress Protection rating of 65 but if the valve is to be situated outside or in damp conditions suitable protection should be used. Incorporating electrical surge protection into the system is also advised.Ĭontact with water or other liquids can also damage the coil and cause it to fail. Always check that the electrical supply matches the voltage and frequency of the coil as shown on the coil’s label. Burnt out coils cannot be repaired and will need to be replaced.

Electrical surges or spikes may also damage the coil. Solenoid coil failure can be caused by a number of factors.Īpplying an incorrect voltage to the coil will cause it to fail and may cause the coil to burn out. Impurities entering the valve may damage the internal components and cause the valve to malfunction. If the media contains sediment or particles a filter should be fitted upstream of the solenoid valve to prevent contamination of the valve’s components. This should reduce the risk of any sediment in the media falling into the tube and restricting the movement of the armature. Ideally the solenoid valve should be installed with the armature tube pointing upwards. Some solenoid valves will also be marked with an arrow on the body indicating the direction the media should flow. The solenoid valve should be installed with the inlet port (usually marked as port 1) connected to the upstream flow and the outlet port (usually marked as port 2) connected to downstream. The effect on these temperatures caused by connected or nearby equipment should also be considered before installation. disc located at the top of the armature tube, and is usually measured in bar.Įnsure that the media is compatible with both the construction material of the valve and the seal material.Ĭheck that the media and ambient temperatures are within the minimum and maximum temperature rating of the solenoid valve. The pressure rating of the valve can be found on the I.D.
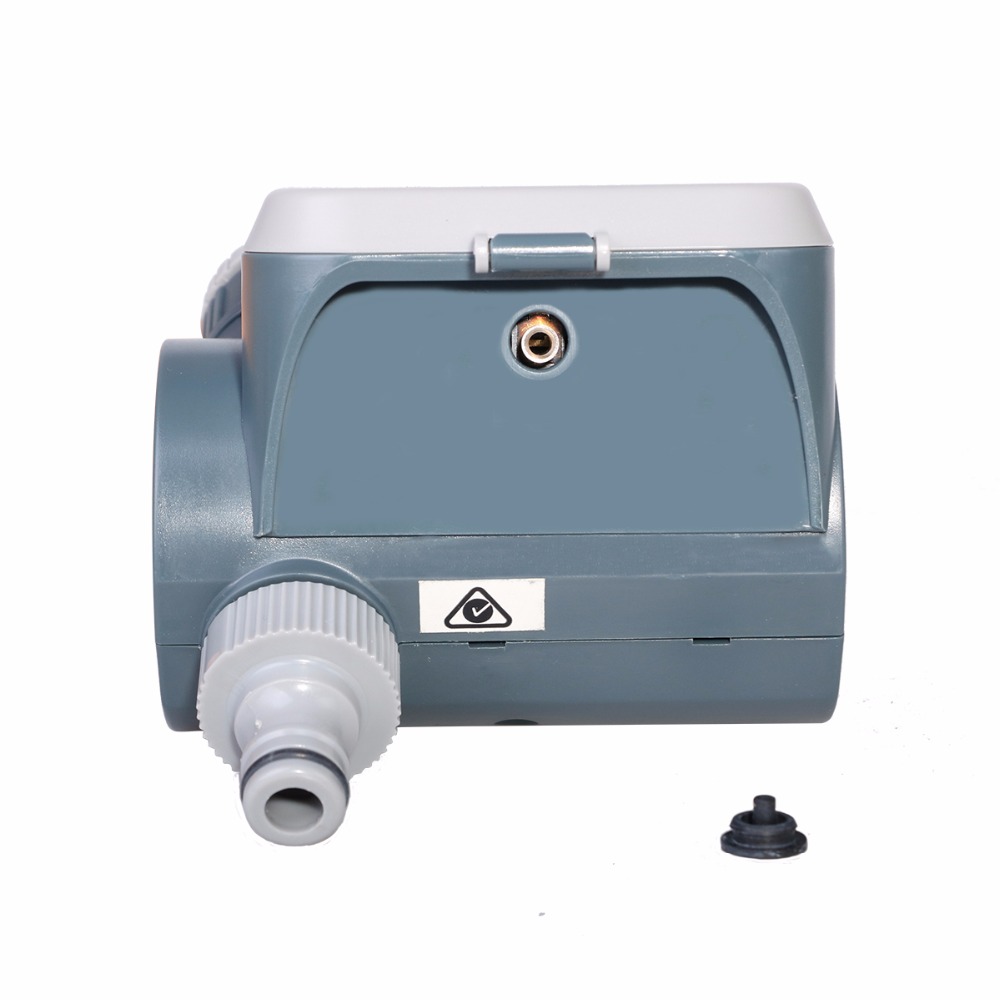
Pilot operated solenoid valves and assisted lift solenoid valves also have a minimum pressure rating which must be met for the valve to function correctly. Make sure that the pressure of the media that is to pass through the solenoid valve does not exceed the maximum pressure rating of the valve. This can be found on the label on the side of the coil. John deere 345 coolant change.Before installing a solenoid valve into a system consider the following points.Ĭheck that the voltage supply matches the allowed voltage of the solenoid coil.
